The latest news about SDM
We invite you to learn more about our programs by reading our latest news or joining us at one of our upcoming info sessions, webinars, or special events.
Filter By:
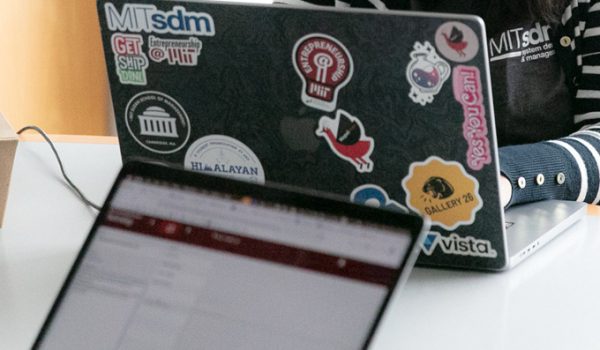
by Stefanie Koperniak Three SDM fellows have had the opportunity to use and expand upon what they have been learning in SDM as part of the Social and Ethical Responsibilities
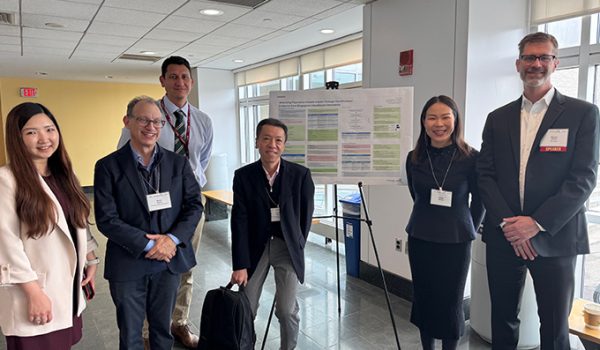
Written by SDM fellows Jonas Urbonas, Mohammed Alsehali, Ben Arocho, Lal Bahadur, Michal Delkowski, Matt Mohler, and Myles O’Brien Day 1 On Wednesday, March 5, Wong Auditorium
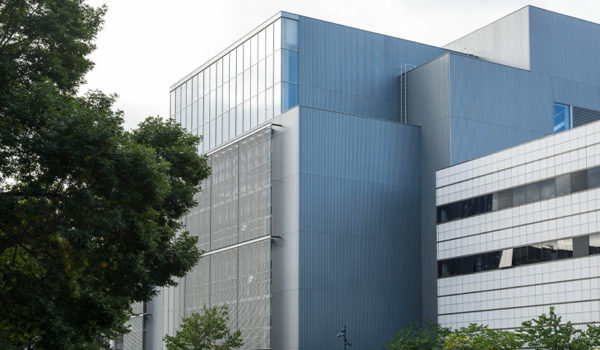
System Design and Management is a sponsor of the MIT Sloan New Space Age Conference, scheduled for Friday, April 25, 2025 at the MIT Media Lab in Cambridge, MA. This
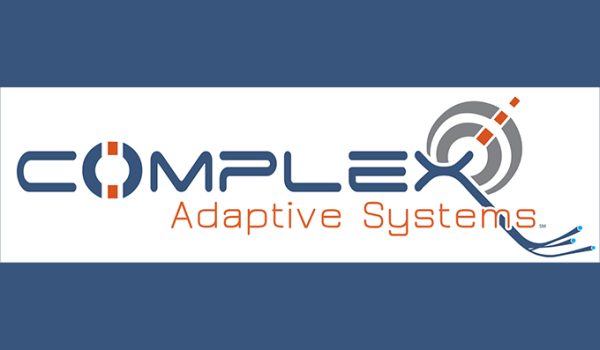
MIT System Design and Management will host Complex Adaptive Systems 2025 from March 5–7, 2025, on the MIT campus in Cambridge, MA. The conference is supported by the New England
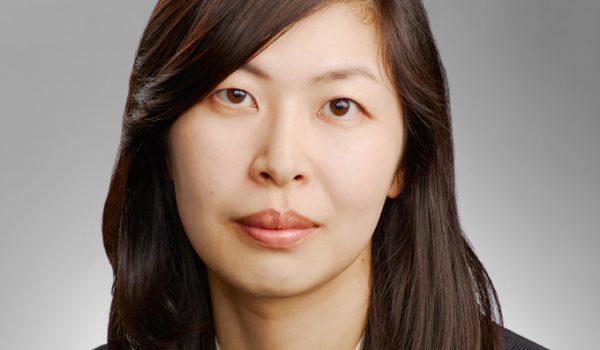
MIT System Design and Management (SDM) has named Ayako Yukawa the winner of the SDM Best Thesis Award for 2024. Her thesis, titled “Architecting Absorptive Capacity: Systems
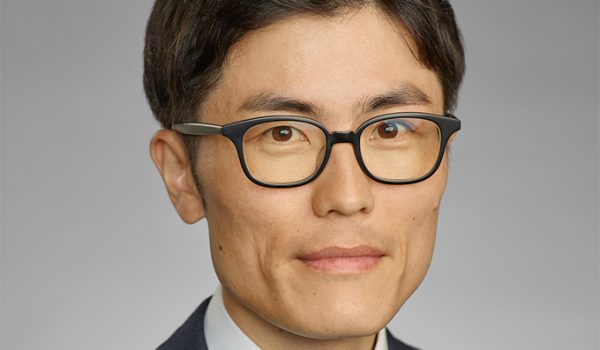
Hiroki Ogasawara is the 2024 recipient of the MIT SDM Student Award for Leadership, Innovation, and Systems Thinking. Hiro’s extensive service and efforts in a range of
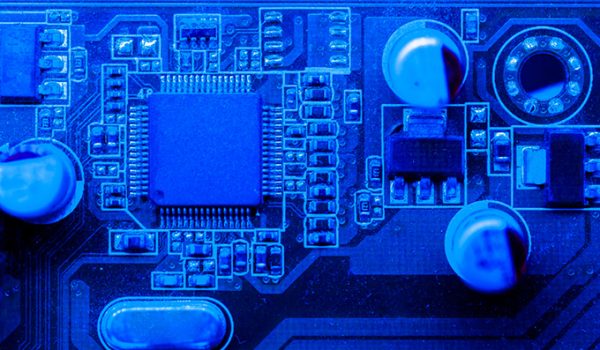
by Stefanie Koperniak When Ben Linville-Engler attended an event for the groundbreaking of a new MITRE bluetech facility in November 2021, he went on a tour led by Moise Solomon,
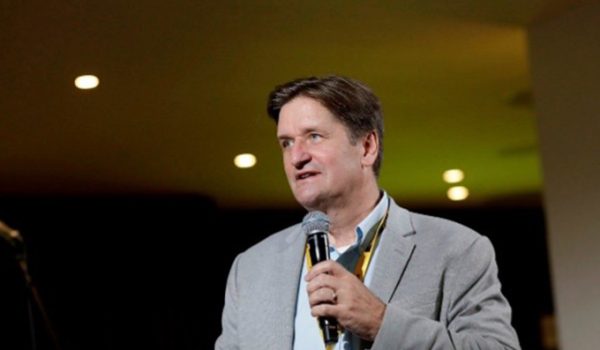
Bryan R. Moser, academic director and senior lecturer in System Design and Management at the Massachusetts Institute of Technology, has been elected president of the International
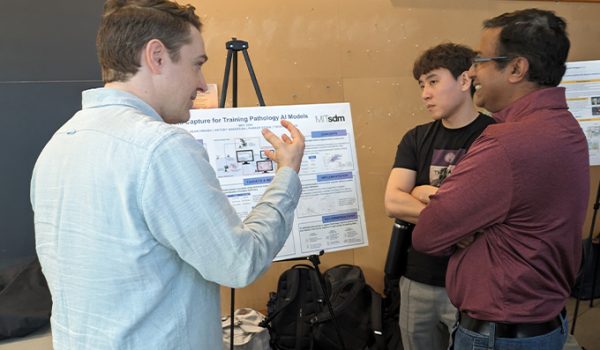
At MIT System Design and Management, one of our strongest assets is our network of project partners. These organizations include non-profits, companies, and governments, who come
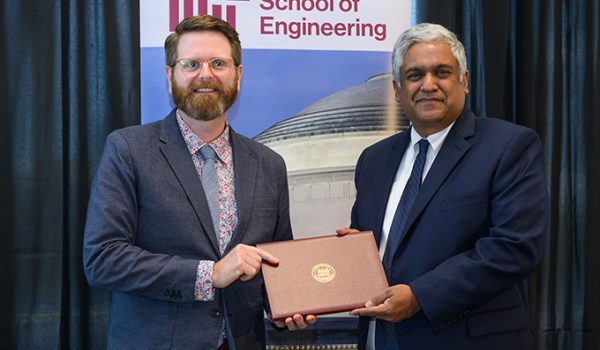
Steven Derocher, senior IT manager for the LGO and SDM programs, has received an Infinite Mile Award from the School of Engineering. This award, given annually, recognizes